These days, with natural resources declining and environmental pollution rising, people are starting to pay increasing amounts of attention to how waste is disposed of. The waste recycling industry is now big business. To invest in a waste recycling plant is very profitable. Following is a brief tyre pyrolysis plant project report.
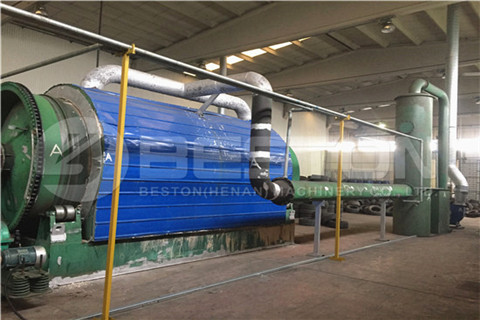
In Japan, the US and the EU alone over six millions tons of scrap tires are discarded annually. The massive quantities of waste tires being discarded in the world are only set to increase as the automotive industry continues to expand. The disposal of waste tires has become a serious environmental issue. When tires are sent to landfills, the toxins they contain leak into the environment. Furthermore, tires posse a big fire risk on landfill sites as methene gas can gather inside of them. Rubber can take over 80 years to decompose. The impact of waste rubber in landfill sites can be minimized by choosing to recycle that rubber tire into energy using the latest pyrolysis technology.
The good news is that in 1990, over 62% of landfill waste in EU countries was waste tires, and that percentage is now in single digits as a result of EU legislation. Now, most tires are incinerated to generate heat. However, the problem with burning tires is that the process produces a lot of environmental atmospheric pollutants. It is hoped that the uptake of tire pyrolysis technology will eventually replace the need for incineration and landfilling of waste tires.
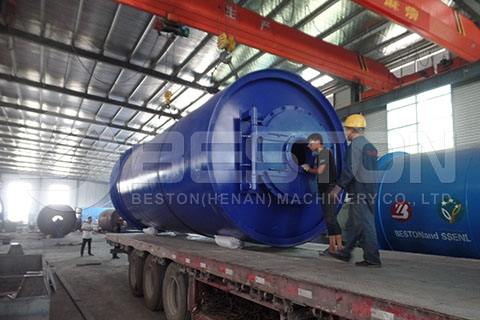
The great thing about tire recycling plants is that they produce zero pollution. What’s more, the reactor furnace can be fuelled by the combustible gases produced during pyrolysis, so the process is incredibly energy-efficient. Carbon black, fuel oil and combustible gases are some of the end products produced from tire pyrolysis. With further refinement in a distillation machine, pyrolysis oil can be converted into more marketable fuels like gasoline. The percentage of pyrolysis oil produced from an average tire is 45%. 12% of waste tire material is steel wire. To prolong the life of a pyrolysis reactor, the wire should be removed prior to the shredded tires being fed into the reactor.
Working Processes Involved In A Tyre Pyrolysis Plant
To begin with, the steel wire is removed from the waste tires and they are shredded into tiny pieces using a grinding machine. The raw material then enters the oxygen-free reactor chamber. Once the temperature increase the reactor reaches 280 degrees, tire oil vaporizes. As the temperature continues to increase, oil vapor of different viscosities is produced. A condensing separating device is used to separate light and heavy components. The vapor that is liquified is rubber oil. The non-liquefied vapor is combustible gas, which is used to reheat the reactor.
Tyre Pyrolysis Plant Technical Specifications
Tire pyrolysis plant from different manufacturers has different technical specifications. Some reactors have a batch working method, while others are fully continuous. In addition to processing waste tires, pyrolysis reactors can also process a wide range of other waste materials including rubber, oil sludge, waste plastic, industrial sludge and more. More details can be found: https://beston.co.za/waste-tyre-pyrolysis-plant/.