Innovative continuous pyrolysis plant design is a new concept in the field of waste treatment, which can be divided into two categories: batch and continuous. The batch type is the traditional design, in which the feedstock is charged into a reactor and then pyrolyzed.
After the reaction is complete, the product gas is discharged from the top of the reactor, while the solid residue remains at the bottom. In contrast, the continuous type pyrolysis plant (planta de reciclaje de neumaticos) does not have a reactor; the feedstock is fed into one end of a long, sealed tube, and pyrolyzed as it moves slowly through the tube. The product gas is drawn off from the other end of the tube, while the solid residue accumulates on the inside wall of the tube.
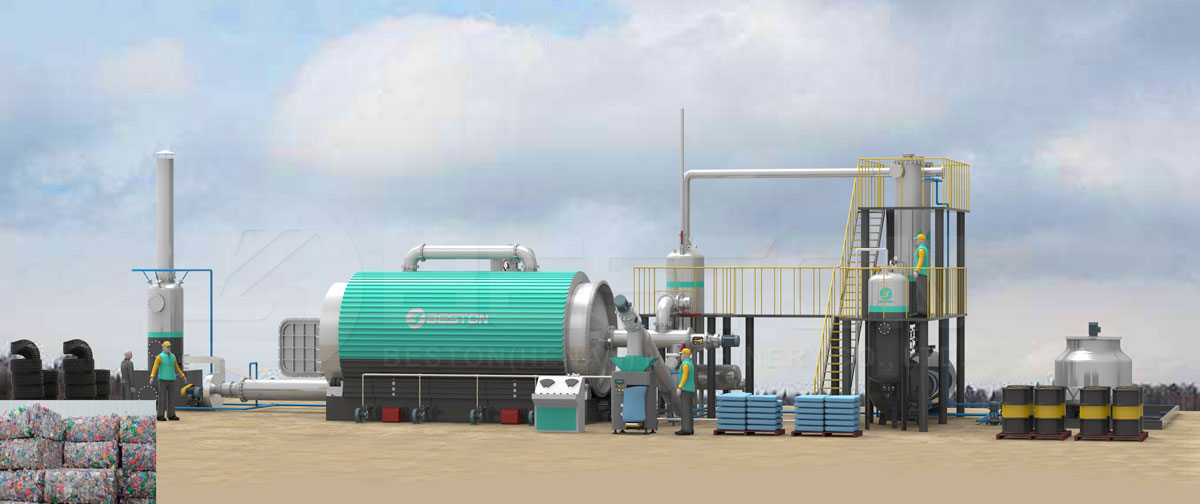
The advantages of a continuous pyrolysis plant (https://www.bestoneco.com/planta-de-pirolisis-continua/) design may include but are not limited to:
Continuous Feedstock Supply
The feedstock can be supplied continuously, eliminating the need to stop and start the pyrolysis process. This makes continuous pyrolysis plants suitable for large-scale production.
Efficient Heat Transfer
In a continuous process, the feedstock is in contact with the hot reactor wall for a more extended time than it would be in a batch plant (planta de pirolisis)design, resulting in better heat transfer efficiency and improved reaction rate. This means that lower temperatures can be used in a continuous plant, which reduces energy consumption. This is particularly beneficial for waste treatment, where low energy costs and high efficiency are essential.
Higher Capacity
Because the continuous process spends more time in contact with the reactor wall than a batch design would, it can handle larger loads of feedstock per hour. For example, an average-sized plant using traditional pyrolysis technology might be able to produce about 15 kg of product gas per hour. However, a continuous pyrolysis plant with the same reactor size could produce up to 60 kg of product gas per hour.
Reduced Pollution
The continuous design also results in less pollution than the batch design. The solid residue accumulates on the inside wall of the tube rather than at the bottom of the reactor, which means that there is less chance of it coming into contact with the product gas. This reduces the number of pollutants that are released into the atmosphere.
Reduced Operating Costs
The continuous pyrolysis plant (Maquinaria Beston)design also results in reduced operating costs. The lower energy requirements mean that less fuel is needed to run the plant, which helps to keep costs down. In addition, there is no need for a cooling system or gas storage facility, which reduces maintenance and capital expenses.
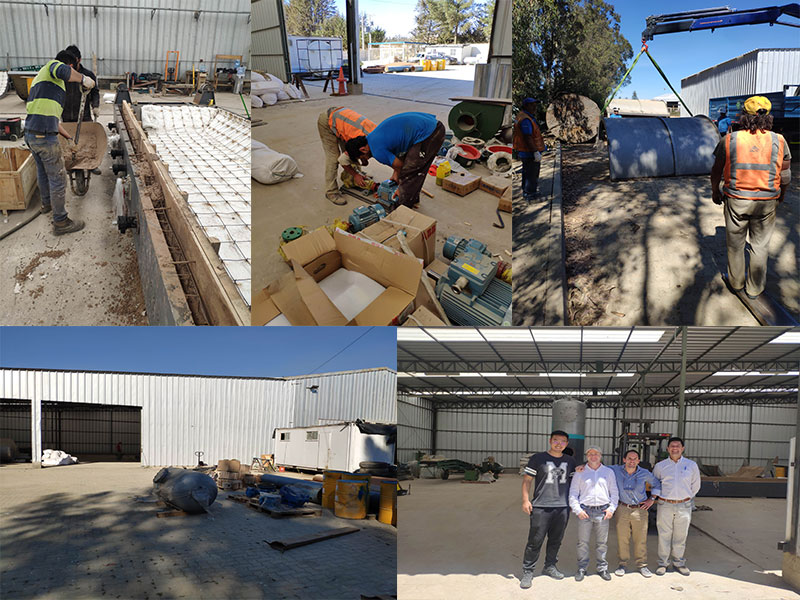
Continuous Control over Temperature and Reaction Rate
One key benefit of continuous pyrolysis plants is that temperature control can be more precise than in batch plants because there are no “dead zones” or stagnant areas where heat transfer is poor. This allows for better product quality and reduced emissions.
The benefits of a continuous pyrolysis plant design are numerous and can include improved reaction rate, heat transfer efficiency, product quality, and reduced emissions. These plants are well suited for large-scale production and require less energy to operate than traditional batch pyrolysis plants. Continued advances in this technology will undoubtedly lead to even more efficient and effective production methods.