Crude oil sludge is a product of exploration, drilling, and refining of crude oil. Oil, water, and sludge are the main components. These substances can cause environmental degradation if they are not disposed of properly. Crude oil sludge is a major waste product from refining and petrochemical operations that needs to be treated. It has a large percentage of combustible substances that have high heating properties.
Currently, crude oil sludge is mostly disposed of through landfills or immobilization which needs a large amount of space and poses a pollution threat to groundwater and the soil. Using a pyrolysis plant to convert crude oil sludge to valuable compounds like carbonaceous residue and molecular organic compounds enables useful resource utilization and eliminates the disposal problem.
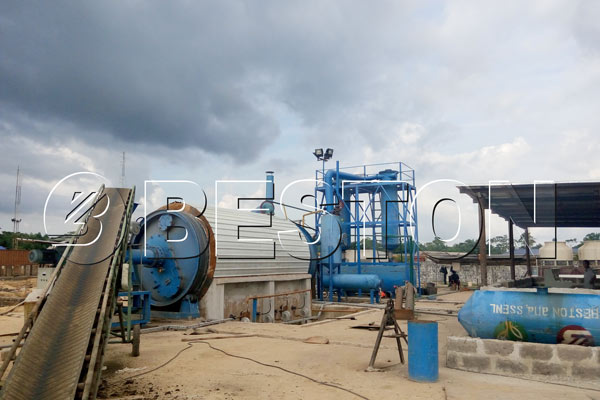
Components of a Crude Oil Sludge Pyrolysis Plant
A typical crude oil sludge pyrolysis plant consists of the following main components; a feeder mechanism, oil gas filter, recycling system, pyrolysis reactor, discharging system, powerful spray dedusting system, spray cooling component, temperature and pressure monitors, and a centralized electrical control system.
Oil Sludge Pyrolysis Treatment Process
1. Drying
First, the crude oil sludge is dried to reduce the energy and time required during pyrolysis.
2. Pyrolysis.
The crude oil sludge is poured into the pyrolysis reactor. The temperature is increased to above 200 degrees, which enables oil gas to be produced. As this process proceeds, the manifold sets apart the heavy oil and light oil. The lighter oil ascends into the condenser where it is liquefied and then transferred to a collection tank. On the other hand, the heavy oil accumulates in the residual tank from where it can be pumped back into the pyrolysis reactor using an oil pump. The process can also be used to dispose of waste tyres, which you can find more details at https://www.bestongroup.com/tyre-to-oil-plant-cost/.
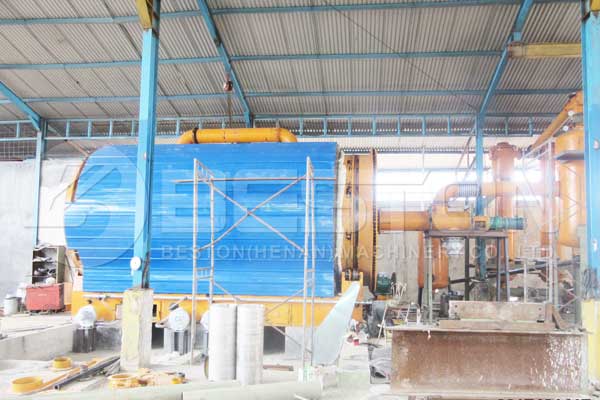
Benefits of Using a Pyrolysis Plant
1. Security
Most pyrolysis plants are fully equipped with safety features to enable simple and safe operation. Each reactor contains safety and thermo-detector valves to ensure maximum safety.
2. Environment-Friendly
Plants with advanced dedusting systems can control the tail gas productively to effectively comply with emission standards and enable green production.
3. Durability
The materials used in constructing the plant consist mainly of stainless steel welded together automatically using the latest X-ray weld technology. Also, since the heating is done indirectly the life of the pyrolysis reactor is extended. This allows the plant to last for up to 15 years depending on the actual operation.
4. Energy Savings
The heating system is completely sealed to eliminate the possibility of gas leaking and to save energy. The additional gas is recycled into the plant and heated in a vacuum to generate very strong negative pressure. In these settings, the crude oil sludge will pyrolyze quickly without using a lot of energy.
End Products and Their Uses
The end products are usually water, fuel oil, and solid waste. How can these products be used? If the fuel oil is extremely pure it can be directly utilized as a fuel. Also, you can use waste oil distillation to further refine it and convert it into diesel. When it comes to solid waste it can be effectively used to produce various kinds of construction materials.
Crude oil sludge contains a lot of oil and it can be converted from a disposable waste to a valuable income source. Since oil sludge is a pollutant that can harm the environment, affected organizations such as governments and private companies need to invest in the Beston pyrolysis plant. It will be worthwhile. One, it will generate precious fuel oil that can be sold or used internally. Second, it will eliminate the risk of punitive costs associated with pollution offenses.